Product Search
Crusher Series
Home > Products > Crusher Series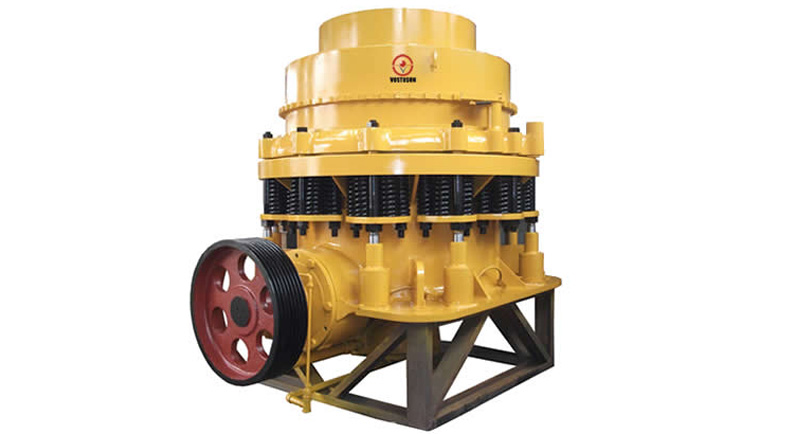
Symons Cone Crusher
The Symons Cone Crusher of VSG series is widely used in the industries of metallurgy, building material, road construction, chemical engineering and silicate. It is suitable for crushing all kinds of ores and rocks with hardness of medium or above. The crushers has the feature of high crushing ratio,
We're here to help
Easy ways to get the answers you need.
Contact Now
- TEL:0086-21-68406143-802
- FAX:0086-21- 68406146
- Email:[email protected]
The Symons Cone Crusher of VSG series is widely used in the industries of metallurgy, building material, road construction, chemical engineering and silicate. It is suitable for crushing all kinds of ores and rocks with hardness of medium or above. The crushers has the feature of high crushing ratio, high efficiency, high capacity, low operating cost and easy adjustment. The qualified material for components and reasonable design of construction contribute to its longer running performance and even granularity of end product and reduction of the circulation load. Furthermore, by adopting the hydraulic cleaning chambers system, the down time reduced. As there are many types of chambers of the cone crusher, customers can choose the most suitable one according to the requirement.
Advantages:
1. Overall Performance:
A. We are professional and we can produce them in large quantities. Moreover, the main parts are also processed by us. We have specialized machines which can assure the data. The crusher can perform better when we strictly produce it in accordance with the accuracy of the drawing.
B. According to the principle of the designs, when the intersection point of two centerline of eccentric sleeve coincides with the center of the spherical body, the crusher can work steadier and have the largest broken torque.
C. In respect of manufacturing cone gear, the gears are casted by 40Cr arc furnaces and the pinions are forged by 35SiMn.
D. As to the core parts of the cone crusher, the precise of the eccentric sleeve decide the accuracy of kinematic link of the whole set of machine. Each specification of the eccentric sleeve is produced by different equipments.
2. Cleaning cavity: Eight hydraulic cylinders reduce the oil press of the hydraulic system so that it will have little oil spill.
3. Locking: In order to make the locking system more reliable, the crusher is locked by both the spring and hydraulic cylinders.
Working Principle:
When it is working, the motor drives the eccentric bearing bushing via spring coupling, transmission shaft and a couple of cone gear wheel. The crushing cone axis is forced to swing by the eccentric bearing bushing, which makes the mantle sometimes be close to the bowl liner, and sometimes far away from the bowl liner, so that raw materials are pressed, impacted and crushed in the crushing chamber.
Crushing Materials:
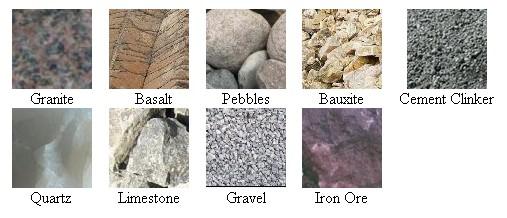
Two kinds of Crushing Cavity of Symons Cone Crusher:
The crushing cavity of Symons cone crusher including: standard and short head.
1. Standard cone crusher: The major difference between Standard and Short Head Symons cone crusher is the shape of the crushing cavities.
2. Standard cone crushers are designed to make a product ranging from ½″to more than 2½″in both open and closed circuits. They may be furnished with fine, medium, coarse and extra coarse cavities to meet variations in size of input and output product.
Standard cone crushers may be applied to large or small operations for single reduction, or as a primary or secondary crusher ahead of Short Head machine. Six sizes are available from 2 to 7’’ in diameter. Open circuit capacities range from 18 to over 1500net tons per hour.
3. Short Head cone crusher: Symons Short Head cone crushers have a steeper head angle and a more parallel crushing cavity than Standard one. They are designed for smaller input and output product. Particle size is from 5mm to 25mm in both open and closed circuits.
Short Head crushers are available in six sizes from 2 to 7’’ in diameter and with the capacity 720t/h. Of course, we can design cavity according to your requirement.
Maintenance:
1. The materials must be feed in the middle of the distributor. It is not allowed to feed the materials into the crushing chamber directly, because that will make the crusher overloaded and the liner plate will be abraded unevenly. Correct feeding way:
a. The materials are distributed equally to the crushing chamber.
b. The quantity of materials should not higher than the mortar.
2. The max feeding size should not equal to the feed opening, (the max feeding size=85% of the feed opening) otherwise, it will lead to:
a. The capacity is low.
b. Some spare parts will be damaged.
3. The crusher is not allowed to start in overload condition in case of accident.
4. When stop the crusher, stop the feeder first. After all materials are discharged out, stop the crusher.
5. The locking system and hydraulic station should be checked to avoid problems.
Factors to Enhance Capacity:
1. Proper selection of crushing chamber according to raw materials.
2. Proper percentage of the particle sizes.
3. Control feed rate.
4. Feed material evenly.
5. Conveyor can meet maximum capacity of the crusher.
6. Proper circuit.
7. Automation controls.
8. Adequate area for discharging.
Guarantees:
1. Assist clients to prepare for the first construction scheme;
2. Install and debug the equipment;
3. Examine the equipment regularly;
4. Take initiative to eliminate the troubles rapidly at site;
5. Supply accessories;
6. Provide technical exchanging;
7. Provide maintenance.
Advantages:
1. Overall Performance:
A. We are professional and we can produce them in large quantities. Moreover, the main parts are also processed by us. We have specialized machines which can assure the data. The crusher can perform better when we strictly produce it in accordance with the accuracy of the drawing.
B. According to the principle of the designs, when the intersection point of two centerline of eccentric sleeve coincides with the center of the spherical body, the crusher can work steadier and have the largest broken torque.
C. In respect of manufacturing cone gear, the gears are casted by 40Cr arc furnaces and the pinions are forged by 35SiMn.
D. As to the core parts of the cone crusher, the precise of the eccentric sleeve decide the accuracy of kinematic link of the whole set of machine. Each specification of the eccentric sleeve is produced by different equipments.
2. Cleaning cavity: Eight hydraulic cylinders reduce the oil press of the hydraulic system so that it will have little oil spill.
3. Locking: In order to make the locking system more reliable, the crusher is locked by both the spring and hydraulic cylinders.
Working Principle:
When it is working, the motor drives the eccentric bearing bushing via spring coupling, transmission shaft and a couple of cone gear wheel. The crushing cone axis is forced to swing by the eccentric bearing bushing, which makes the mantle sometimes be close to the bowl liner, and sometimes far away from the bowl liner, so that raw materials are pressed, impacted and crushed in the crushing chamber.
Crushing Materials:
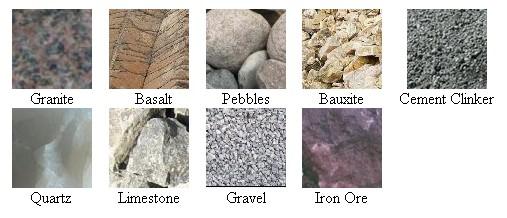
Two kinds of Crushing Cavity of Symons Cone Crusher:
The crushing cavity of Symons cone crusher including: standard and short head.
1. Standard cone crusher: The major difference between Standard and Short Head Symons cone crusher is the shape of the crushing cavities.
2. Standard cone crushers are designed to make a product ranging from ½″to more than 2½″in both open and closed circuits. They may be furnished with fine, medium, coarse and extra coarse cavities to meet variations in size of input and output product.
Standard cone crushers may be applied to large or small operations for single reduction, or as a primary or secondary crusher ahead of Short Head machine. Six sizes are available from 2 to 7’’ in diameter. Open circuit capacities range from 18 to over 1500net tons per hour.
3. Short Head cone crusher: Symons Short Head cone crushers have a steeper head angle and a more parallel crushing cavity than Standard one. They are designed for smaller input and output product. Particle size is from 5mm to 25mm in both open and closed circuits.
Short Head crushers are available in six sizes from 2 to 7’’ in diameter and with the capacity 720t/h. Of course, we can design cavity according to your requirement.
Maintenance:
1. The materials must be feed in the middle of the distributor. It is not allowed to feed the materials into the crushing chamber directly, because that will make the crusher overloaded and the liner plate will be abraded unevenly. Correct feeding way:
a. The materials are distributed equally to the crushing chamber.
b. The quantity of materials should not higher than the mortar.
2. The max feeding size should not equal to the feed opening, (the max feeding size=85% of the feed opening) otherwise, it will lead to:
a. The capacity is low.
b. Some spare parts will be damaged.
3. The crusher is not allowed to start in overload condition in case of accident.
4. When stop the crusher, stop the feeder first. After all materials are discharged out, stop the crusher.
5. The locking system and hydraulic station should be checked to avoid problems.
Factors to Enhance Capacity:
1. Proper selection of crushing chamber according to raw materials.
2. Proper percentage of the particle sizes.
3. Control feed rate.
4. Feed material evenly.
5. Conveyor can meet maximum capacity of the crusher.
6. Proper circuit.
7. Automation controls.
8. Adequate area for discharging.
Guarantees:
1. Assist clients to prepare for the first construction scheme;
2. Install and debug the equipment;
3. Examine the equipment regularly;
4. Take initiative to eliminate the troubles rapidly at site;
5. Supply accessories;
6. Provide technical exchanging;
7. Provide maintenance.
Model | VS 75-B | VS 160-B | VS 250-B | VS 350-B | |||||||||
Specs | 3Ft 900mm | 4 1/4Ft 1275mm | 5 1/2Ft 650mm | 7Ft 2134mm | |||||||||
Cavity Type | narrow | medium | wide | narrow | medium | wide | narrow | medium | wide | narrow | medium | wide | |
the Smallest Discharge Size Recommended(mm) |
9 | 13 | 25 | 13 | 16 | 25 | 16 | 22 | 38 | 19 | 25 | 38 | |
Corresponding Feeding Size |
B(close side)(mm) | 83 | 159 | 163 | 109 | 188 | 238 | 188 | 213 | 331 | 253 | 303 | 425 |
B(open side)(mm) | 102 | 175 | 178 | 137 | 210 | 259 | 209 | 241 | 368 | 278 | 334 | 460 | |
Capacity(t/h) | 45-91 | 50-120 | 59-163 | 109-181 | 132-253 | 172-349 | 181-327 | 258-417 | 299-635 | 381-726 | 608-998 | 789-1270 | |
Weight(t) | 15 | 26.5 | 43.5 | 67.3 | |||||||||
Motor Power(KW) | 6P-75 | 6P-160 | 6P-250 | 6P-350 | |||||||||
Overall Dimension (mm) | 2865×2000×2190 | 3300×2500×2940 | 4105×3280×3505 | 5110×4270×4350 |
Get Price And Support
Simply complete the form below, click submit, you will get the price list and a representative will contact you within one business day. Please also feel free to contact us by email or phone.
Previous:Spring Cone Crusher
Next:Hammer Crusher